Firstly, what constitutes PCBA manufacturing services?
PCBA manufacturing services involve specialized manufacturers providing PCB assembly and production services for clients. PCBA refers to the assembly of electronic components on printed circuit boards (PCBs), representing the core aspect of electronic products. PCBA manufacturing services typically encompass the following steps:
Component Procurement: Procuring required electronic components such as resistors, capacitors, chips, etc., from reputable suppliers based on the provided Bill of Materials (BOM).
SMT Assembly: Surface Mount Technology (SMT) is employed to place surface-mounted components on the PCB’s surface, followed by soldering techniques like reflow or wave soldering.
DIP Insertion: Components with pins are inserted into the PCB’s through-holes and soldered using methods like wave soldering or manual soldering.
PCBA Testing: The completed PCBA undergoes visual inspection, electrical testing, functional testing, etc., ensuring quality and performance align with client specifications.
Packaging and Shipping: Qualified PCBAs are safeguarded against electrostatic discharge, water damage, dust, corrosion, etc., before safe packaging and shipment.
What are the advantages of choosing PCBA manufacturing services?
Time and Cost Savings: By engaging professional PCBA manufacturers who handle material procurement, equipment, and personnel, clients save time and costs by simply providing design files and requirements.
Enhanced Quality and Efficiency: PCBA manufacturers possess specialized technology and equipment ensuring quality and efficiency, avoiding errors and issues that clients might face in self-producing PCBAs.
Reduced Risk and Pressure: With comprehensive management and service, PCBA manufacturers assume production risks and responsibilities, alleviating clients’ production pressures and burdens.
While, as PCBA represents a critical part of the product, how to manage or prevent contract manufacturers from using substitute materials that could lower product quality or fail to meet client requirements? To prevent such occurrences, consider the following measures:
1.Select reputable contract manufacturers, sign stringent contracts and confidentiality agreements, outlining material lists, process requirements, quality standards, acceptance criteria, breach liabilities, etc.
2. Consent must be obtained from the buyer for the use of any substitute materials.
3. Conduct sample testing on products from the contract manufacturer, compare them with the original design and samples, and promptly address any discrepancies or failures.
4. Establish effective communication and feedback mechanisms to understand the contract manufacturer’s production status and issues, provide necessary support and guidance, and cultivate strong cooperative relationships.
Additionally, controlling the production process is also crucial for PCBA quality.
Implementing processing control during PCBA manufacturing that manages aspects like solder paste, surface mount adhesive, component loss, etc., and standardizing factors such as skill parameters, processes, personnel, equipment, materials, processing testing, workshop environment, etc., all contribute to enhancing SMT and PCBA processing quality. Identifying faulty products in real-time during contract manufacturing and removing them from further processing stages, stringent quality control, and prioritizing quality management are essential for a qualified manufacturing facility. Below, the process control is discussed in detail.
I. Batch Management
Procedures for controlling non-conforming products, including isolation, marking, recording, review, and resolution, should be clearly outlined. Generally, SMT rework should not exceed three times, and component rework should not exceed two times.
II. Equipment Maintenance and Care
Critical equipment should undergo scheduled inspections by dedicated maintenance staff to ensure their continuous optimal condition. Equipment status should be tracked and monitored, problems identified, corrective and preventive measures taken, and timely maintenance and repairs performed.
III. Production Environment
Adequate and stable water, electricity, and gas supply conforming to processing standards.
Environmental factors like temperature, humidity, noise, cleanliness meeting PCBA processing requirements.
Strict electrostatic discharge systems during PCBA processing.
Strict adherence to entry-exit regulations, equipment operation procedures, and process discipline in production workshops.
IV. Production
Adherence to proper placement, correct labeling, orderly material storage in warehouses, classification, and storage of work-in-progress items consistent with records.
CEN PCBA, a professional one-stop PCBA and SMT processing factory, offers electronic OEM processing, PCBA contract manufacturing, and SMT surface mount processing services.
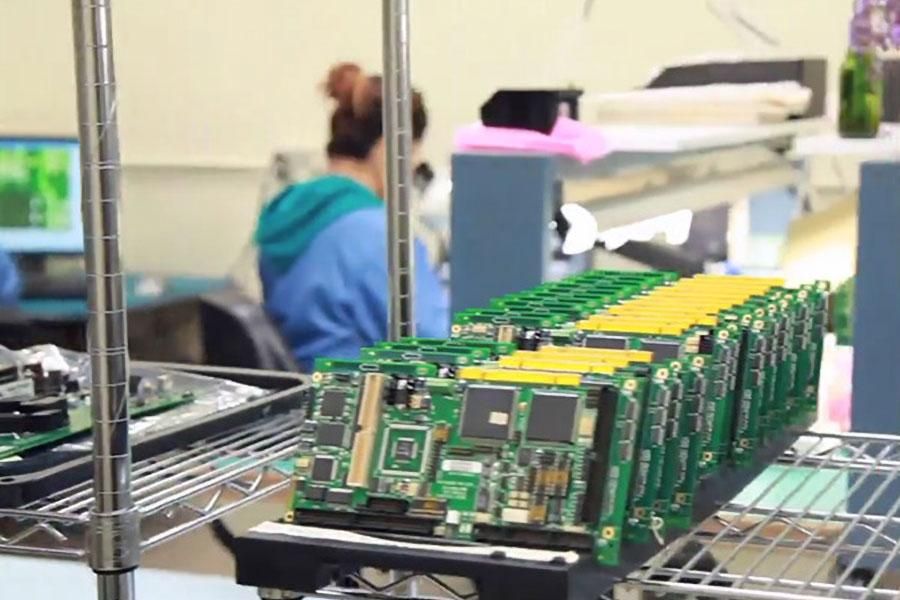